Fasteners and Machining: Enhancing Resilience and Performance in Manufacturing
Fasteners and Machining: Enhancing Resilience and Performance in Manufacturing
Blog Article
Navigating the Globe of Fasteners and Machining: Techniques for Accuracy and Rate
In the complex world of fasteners and machining, the mission for accuracy and speed is a continuous challenge that demands careful attention to detail and critical planning. From understanding the varied selection of fastener kinds to picking optimal materials that can stand up to strenuous demands, each action in the procedure plays a pivotal function in accomplishing the wanted outcome. Precision machining strategies even more elevate the complexity of this craft, needing a fragile equilibrium in between technological proficiency and ingenious techniques. As we dive right into the techniques that can improve both rate and effectiveness in this domain name, the interaction in between quality assurance actions and operational excellence arises as a critical centerpiece.
Understanding Fastener Kind
When selecting bolts for a project, comprehending the various kinds available is critical for guaranteeing optimum performance and dependability. Screws are used with nuts to hold materials with each other, while screws are flexible bolts that can be used with or without a nut, depending on the application. Washing machines are crucial for distributing the tons of the bolt and avoiding damage to the product being secured.
Picking the Right Materials
Comprehending the relevance of selecting the best products is extremely important in guaranteeing the optimum performance and dependability of the selected bolt kinds reviewed previously. When it concerns fasteners and machining applications, the material option plays an essential function in figuring out the total toughness, durability, corrosion resistance, and compatibility with the intended environment. Various products offer varying homes that can significantly impact the performance of the bolts.
Common materials utilized for fasteners include steel, stainless steel, aluminum, brass, and titanium, each having its distinct strengths and weaknesses. Steel is renowned for its high toughness and resilience, making it suitable for a large range of applications. Stainless-steel provides outstanding corrosion resistance, ideal for settings prone to moisture and chemicals. Light weight aluminum is corrosion-resistant and light-weight, making it suitable for applications where weight reduction is important. Brass is commonly selected for its aesthetic allure and exceptional conductivity. Titanium is understood for its phenomenal strength-to-weight proportion, making it suitable for high-performance applications. Choosing the ideal material involves taking into consideration variables such as stamina requirements, ecological problems, and budget restraints to ensure the wanted performance and longevity of the bolts.
Precision Machining Techniques
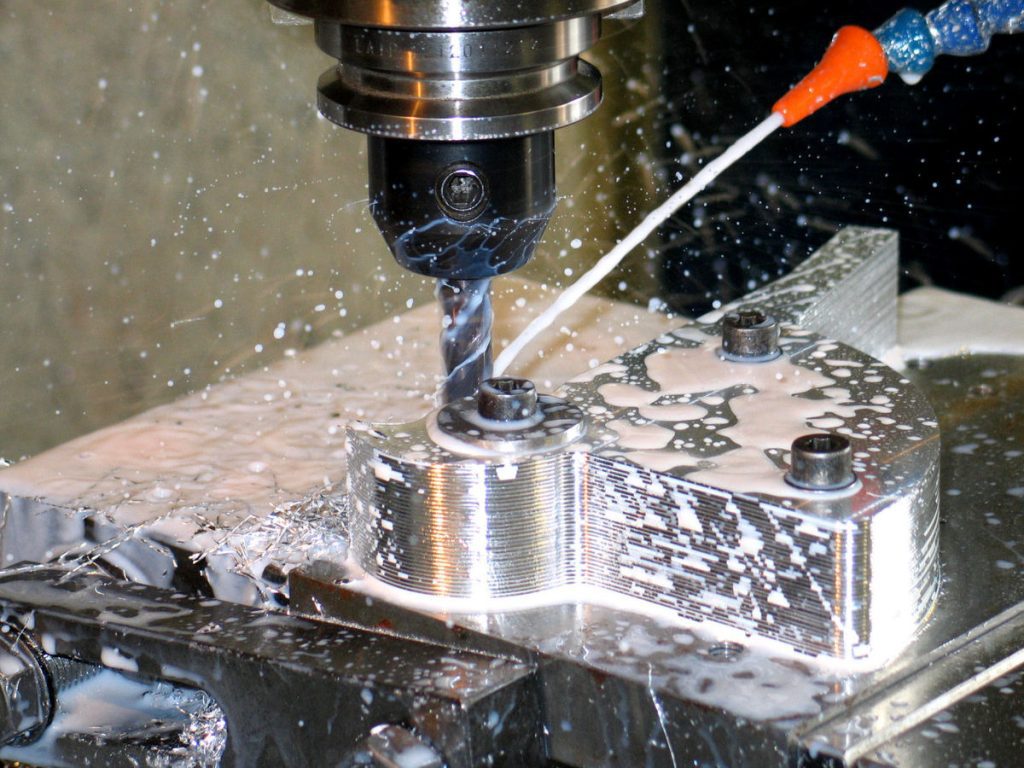
In addition to CNC machining, other accuracy techniques like grinding, turning, milling, and exploration play important functions in bolt production. Grinding assists attain fine surface area finishes and tight dimensional resistances, while transforming is typically made use of to create cylindrical parts with specific sizes. Milling and drilling operations are crucial for shaping and producing openings in bolts, guaranteeing they meet precise requirements and function properly.
Enhancing Rate and Efficiency
To optimize bolt production procedures, it is vital to streamline procedures and carry out effective techniques that complement precision machining strategies. Automated systems can manage recurring tasks with accuracy and speed, enabling employees to focus on even more complicated and value-added tasks. By combining these approaches, producers can attain a balance between rate and precision, eventually improving their affordable side in the fastener market.
Top Quality Control Steps
Implementing rigorous top quality control procedures is crucial in ensuring the integrity and consistency of bolt items in the manufacturing procedure. Fasteners and Machining. Quality control procedures encompass numerous stages, starting from the selection of raw products to the More about the author final examination of the completed fasteners. This entails evaluating factors such as product composition, strength, and durability to assure that the fasteners satisfy sector standards.
Normal calibration of equipment and equipment is critical to preserve uniformity in production and make sure that bolts meet the necessary resistances. Executing stringent methods for determining and resolving problems or non-conformities is vital in protecting against substandard products from going into the marketplace. By developing an extensive high quality control structure, producers can maintain the online reputation of their brand and deliver fasteners that satisfy the highest possible criteria of performance and sturdiness.
Conclusion
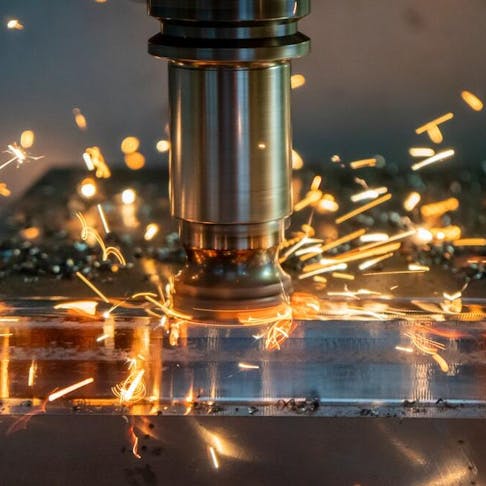
In the elaborate realm of fasteners and machining, the mission for precision and speed is a perpetual difficulty that demands precise interest to detail and critical preparation. When it comes to bolts and machining applications, the product option plays a critical duty in determining the overall toughness, durability, deterioration resistance, and compatibility with the intended environment. Accuracy machining entails numerous innovative techniques that guarantee the tight tolerances and requirements needed for bolts.In enhancement to CNC machining, other precision techniques like grinding, transforming, milling, and exploration play crucial functions in fastener manufacturing.To maximize fastener production procedures, it is essential to streamline procedures and carry out efficient strategies that enhance precision machining techniques.
Report this page